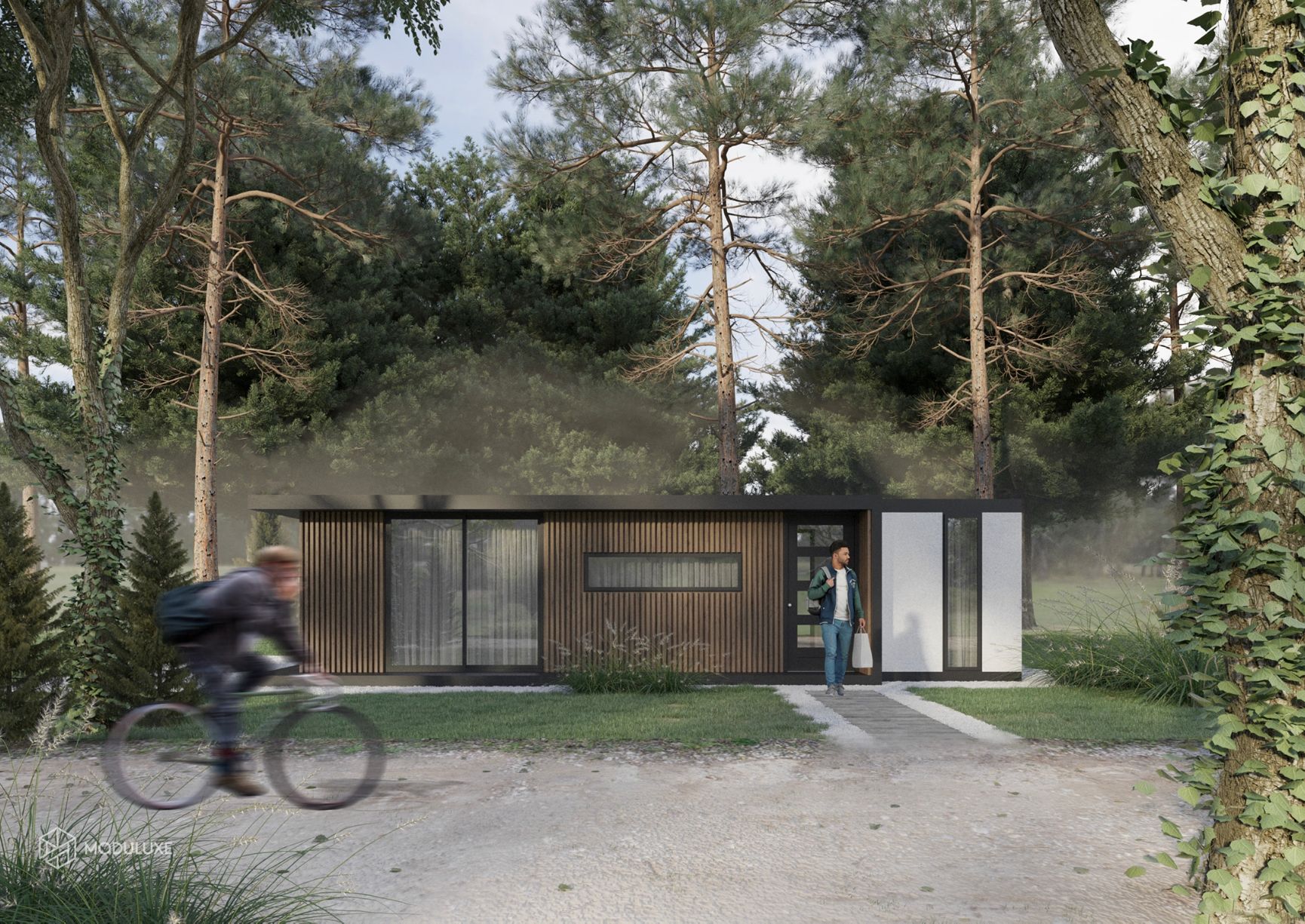
NedPanel
The NedPanel building system is specially designed to greatly simplify the construction of Modular houses. In fact, we have created a modular building element that takes modular building one step further. Simply adding or changing a NedPanel element easily modifies the length or shape of a modular unit.
All-in-one solution
The patented NedPanel building element is more than just a “building block.” This all-in-one solution combines multiple features into a single product:
- Structural Versatility: Functions as a floor, interior and exterior walls, and roof.
- High Insulation Value: Utilizes non-toxic PU/PIR foam that is free from CFK and HCFK.
- Biobased version with customize Bio-Base insolation options.
- Airtight Construction: Designed for optimal airtightness.
- Finishing Flexibility: Interior and exterior walls can be directly finished with nearly all facade materials.
- Fire Resistance: Constructed with A1 Class fire-resistant MgO facade plating.
- Integrated Electrical Cabling: Features plug&play electrical wiring for easy installation.
- Plumbing Integration: Includes both cold and hot water pipes.
- Damp-Proof Barrier: Built-in damp-proof barrier to protect insulation performance.
- Ready for Finishing: Interior and exterior surfaces are primed for immediate application of the final finish layer.
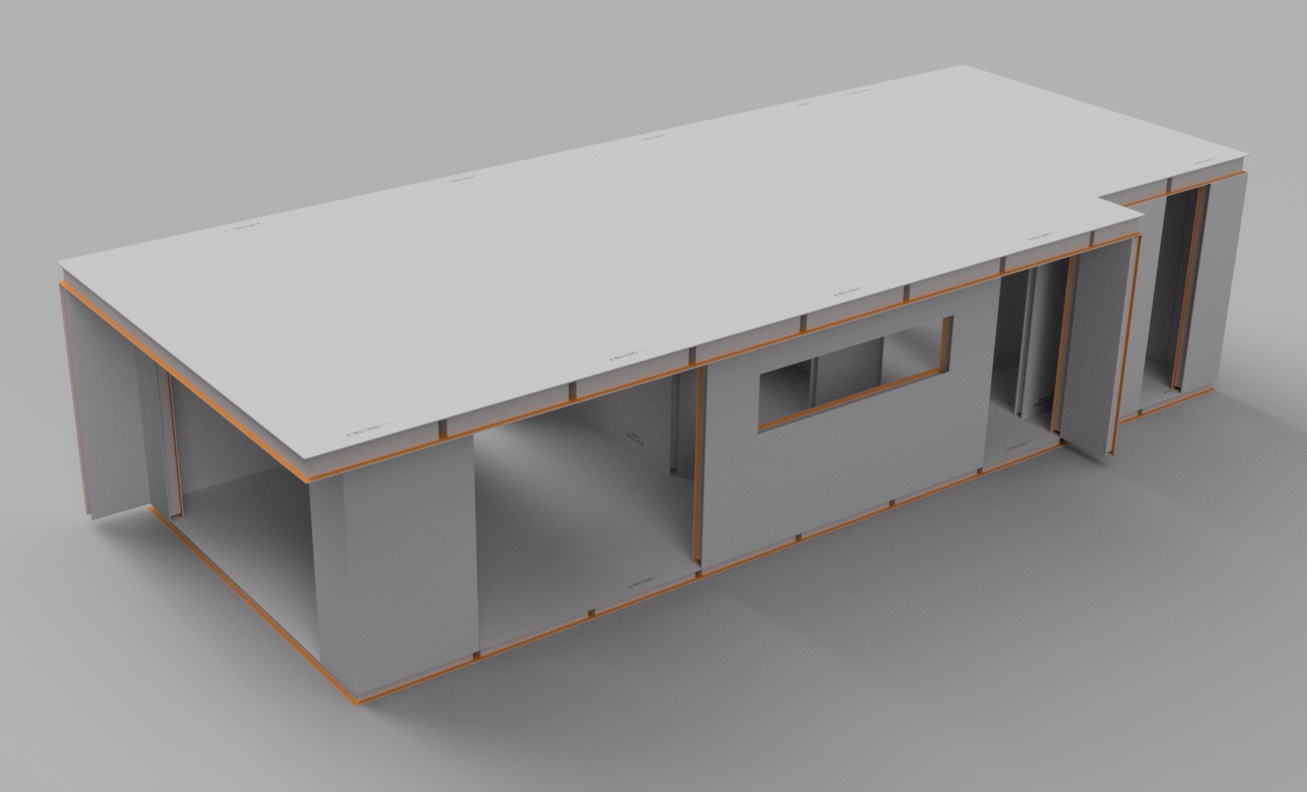
R-SIP Building elements
The NedPanel building elements are so-called ‘Reinforced structural insulated panels’ or in short; R-SIP. The R-SIP panels are standardized in size, include a structural loadbearing frame, offer industry leading insulation values (up to R-value 56, U-value 0,1 W//(m2K), have an integrated damp-barrier and are primer coated to protect the panels during assembly in bad (Dutch) weather conditions. The primer also forms a basecoat for direct application of interior and exterior stucco and glue for façade finishes.
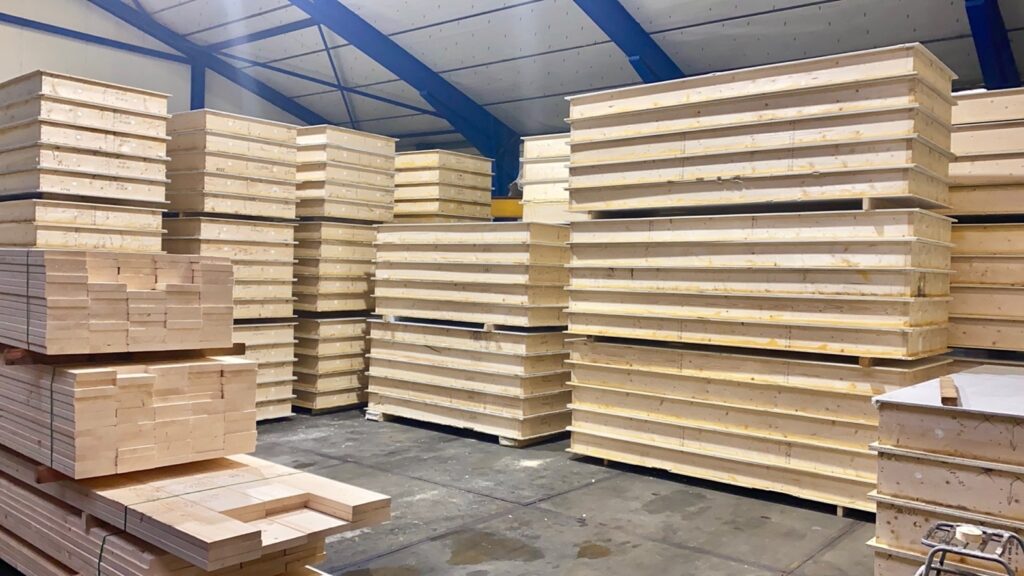
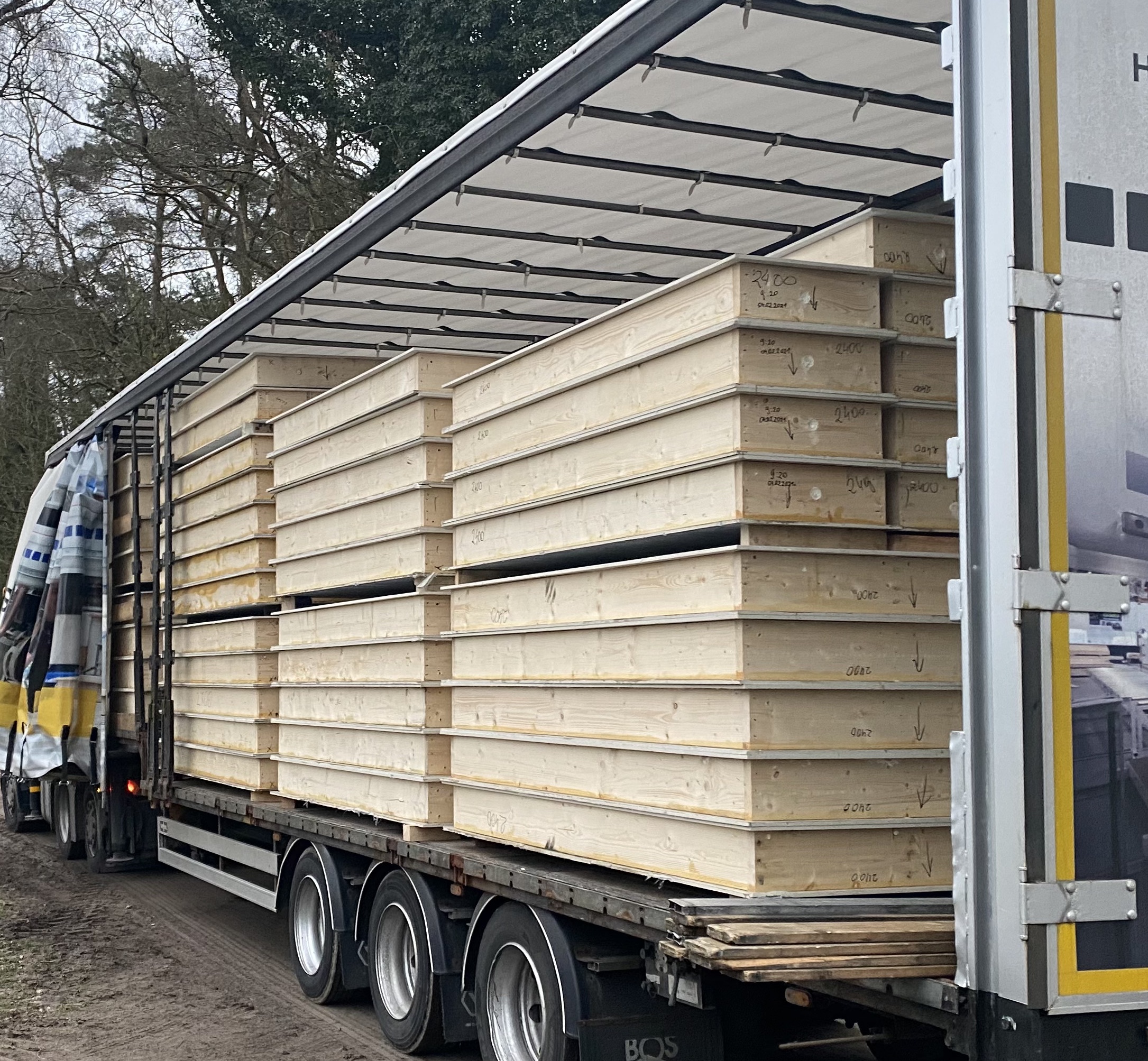
Building with NedPanel R-SIP system reduces not only up to 70% labor hours to finish the house. It also reduces more than 30% of different materials needed to build the house because of the integration of damp control layers, primer coating and technical installation.
The R-SIP elements from NedPanel can be used as wall, roof and floor panels. Because the panel thickness matches the standard construction wood sizes, it is easy to connect with CLS or SLS wood. This is especially useful if extra reinforcement is needed in a wall or suspended floor or roof. If maximum insulation is more important you can use the thermal bridge free NedPanel connector. This connector also is available with an internal 40mm PVC tube that can be used for additional system installation after the house is completed.
Technical Panel system
To streamline onsite construction time, NedPanel has developed a revolutionary system for installations. Our unique solution comprises 18 different technical panels, each equipped with integrated pipes for cold and hot water, drains, and electrical and data cables. Each panel offers a specific Plug & Play installation solution tailored to various applications.For instance, our technical panels are designed for:
- Showers
- Bathroom sinks
- Kitchen appliances
- Toilets
- Light switches
- Smart ventilation systems
- Power sockets
- TVs
- CO2 sensors
- Thermostats
During the design phase or even as late as the construction stage, you can easily position the technical panel in the wall at your desired location. The connections for water and electricity are conveniently located on the roof or elevation floor panel above the technical panel and are concealed with a false metal-stud or MgO ceiling.The simplicity of our Plug & Play installation system allows for quick and easy assembly of NedPanel houses, significantly reducing the need for specialized, hard-to-find, and costly professionals.
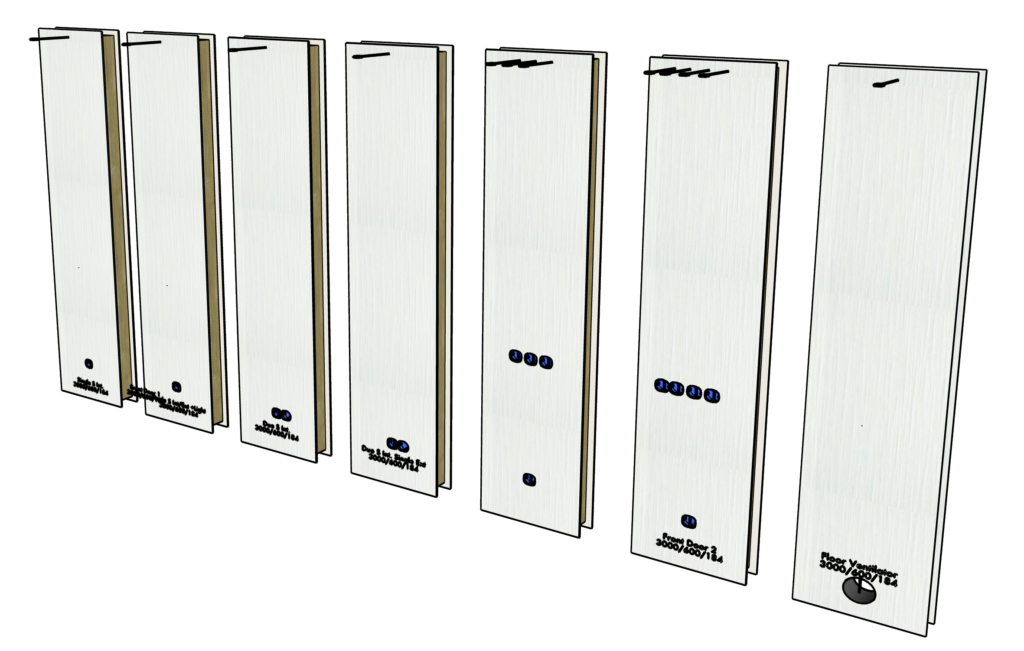
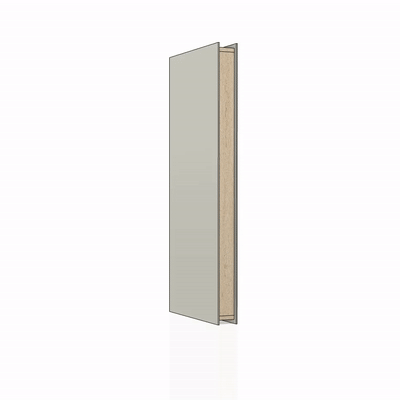
Difference between conventional SIP Element and R-SIP from NedPanel
Conventional SIP (Structural Insulated Panel) elements typically consist of two components: two skin plates on the exterior surrounding a glued or sometimes injected foam core. These panels are commonly made from OSB (Oriented Strand Board) or occasionally from cement-based or composite boards. Each house type requires individual engineering, which is a time-consuming and costly process. For every SIP house design, a custom “kit” must be manufactured by cutting and milling standard-sized SIP panels, resulting in waste due to cutting losses.
In contrast, NedPanel’s R-SIP system revolutionizes this traditional approach. We have streamlined the design by limiting the standard widths of our R-SIP elements to just two sizes: 0.60m (half panel) and 1.20m (full panel), along with fixed standard lengths.
All doors and windows are designed to align with these dimensions, allowing us to create a standardized design method for NedPanel elements that eliminates the need for panel modifications. In close collaboration with our sister company, BetaalbaarWonen BV, we have developed a comprehensive range of Energy+ house designs based on this innovative method.
As a result, we can achieve extremely short lead times for our standard house kits, as all panels can be delivered directly from stock. These stocks can be maintained in partner warehouses, hardware stores, or virtually any location. No other building system offers this level of flexibility, with lead times measured in hours or days rather than weeks or months!
Building with Magnesium, a proven technology
Magnesium oxide (MgO) building products have been extensively utilized in various civil construction projects for over 100 years. However, the use of MgO in construction is relatively new in Europe. In the United States, MgO is widely employed in Florida’s hot and humid climate for building hurricane-resistant homes. Similarly, Japan utilizes MgO construction techniques in regions prone to seismic activity. The lightweight and natural flexibility of MgO structures allow them to better withstand the forces of nature compared to traditionally built homes.
As global warming continues to impact our climate, construction projects face increased exposure to extreme temperature fluctuations, storms, heightened fire risks, and heavy rainfall. Consequently, building codes must be updated to accommodate the demand for more advanced and high-performing construction materials that align with new environmental standards and significantly enhance energy efficiency.
NedPanel leverages MgO construction panels not only to meet these evolving standards but to exceed them substantially. Our commitment to using this innovative material ensures that our buildings are not only resilient but also environmentally responsible.
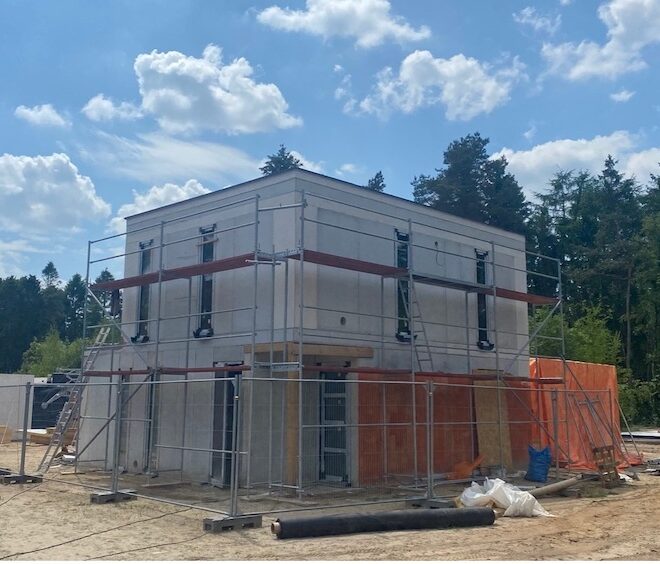
Magnesium oxide (Mgo) As a building material
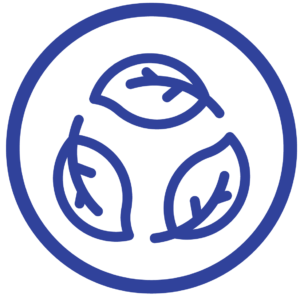
Eco Friendly
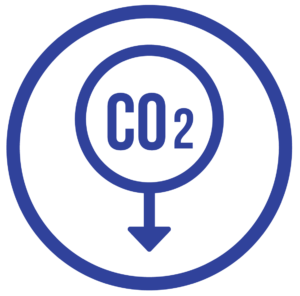
Low Carbon Manufacturing Process
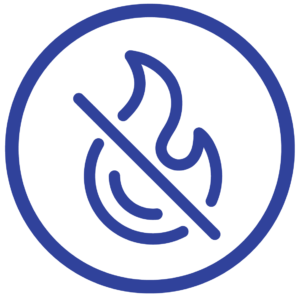
Non Combustible, Non Flammable, Fire Resistant
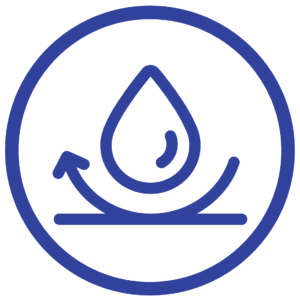
Waterproof
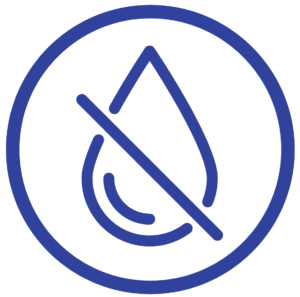
Non Affected by Grease or Oil
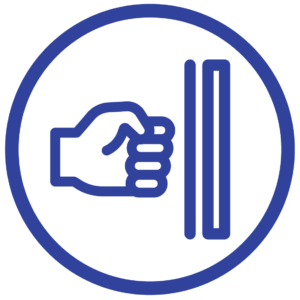
Impact Risistance and High Bending Strenght
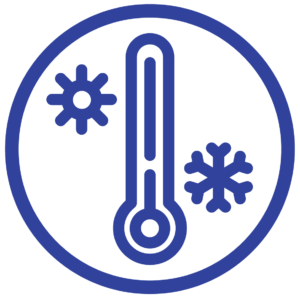
High Resistance to Termal Change
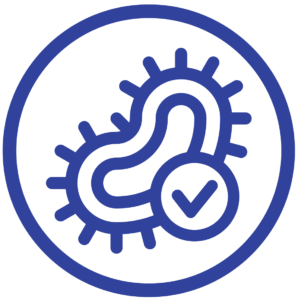
Antimicrobial and Bacteria Resistant
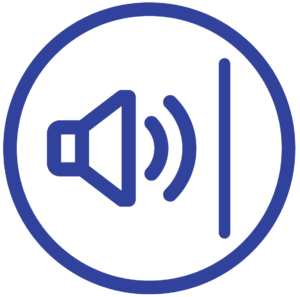
Sound Barries for Walls, Floors and Ceilings
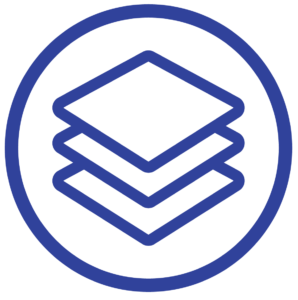
Smooth and Flat Surface, Versatile for finishes
Eco friendly
Magnesium (Mg) constitutes approximately 13% of the Earth’s mass and is a significant component of the planet’s mantle, making it one of the most abundant elements in the Earth’s crust. It is also the third most prevalent element dissolved in seawater, following sodium and chlorine. Known for its green and renewable properties, magnesium is functional and widely used in various modern materials and applications.
NedPanel utilizes reinforced magnesium oxide (MgO) as façade boards, which significantly outperform standard building materials in terms of durability and cost-effectiveness. MgO panels serve as a sustainable alternative to traditional materials such as gypsum, wood panels, Portland cement products, and particularly particle boards (OSB) and plywood. By choosing MgO, we are committed to promoting environmentally friendly construction practices that benefit both our clients and the planet.
Magnesium Carbonite
Magnesium oxide (MgO) is produced through the calcination of magnesium carbonate or magnesium hydroxide. This naturally occurring white solid mineral consists of a lattice structure formed by Mg²⁺ ions and O²⁻ ions held together by ionic bonds. Remarkably, extracting magnesium oxide requires less than one-third of the energy needed for cement production.
The manufacturing process for MgO boards is nearly energy-free. The hardening of these boards occurs through a natural reaction between the components, eliminating the need for ovens; instead, they simply cure in open-air drying stations. This process relies solely on solar energy.
Furthermore, all components used in MgO boards—including magnesium oxide, Lava sand, glass fiber, —are 100% recyclable and environmentally friendly. This makes MgO an excellent choice for sustainable construction projects that minimize environmental impact.
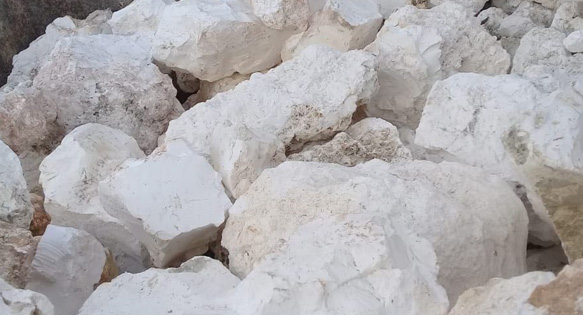